Understanding the High Costs of Building New Homes
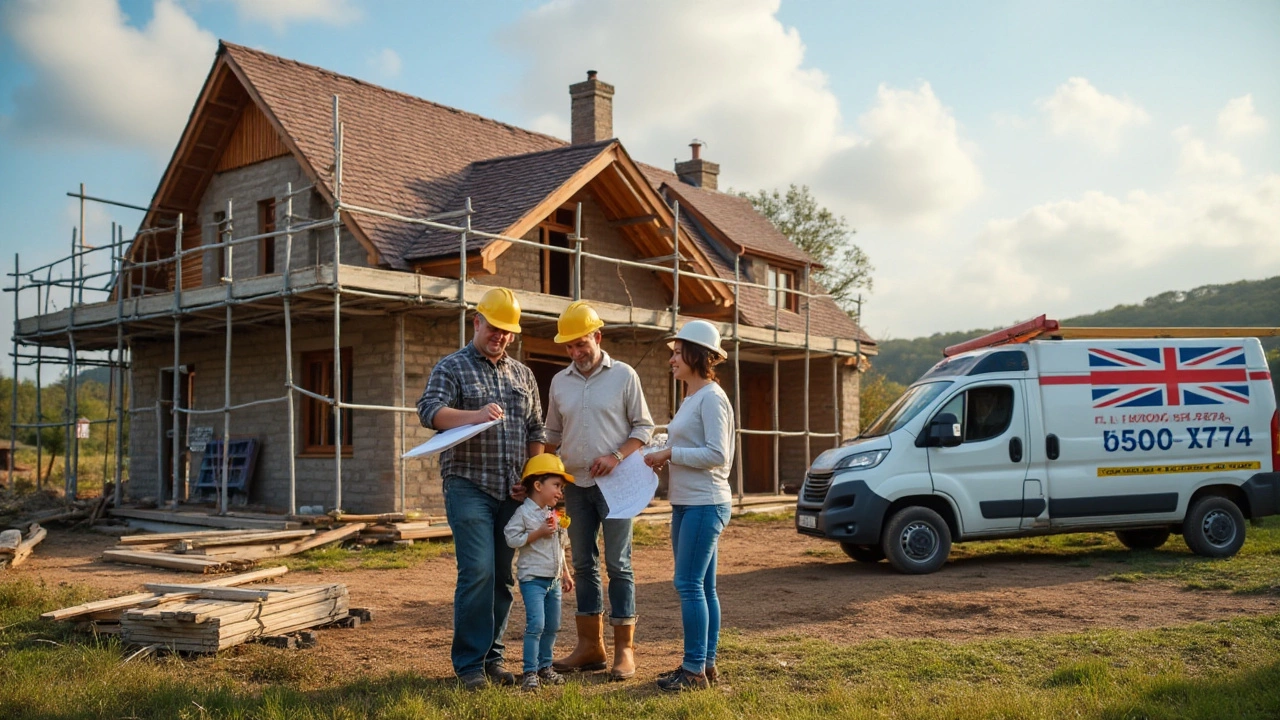
In today's bustling construction market, the dream of building your own house often collides with the stark reality of high costs. Many dreamers find themselves straining under the weight of unexpected expenses, questioning why the financial demands are so steep.
This guide delves into the many reasons behind these rising costs, ranging from the global supply chain disruptions that have impacted material prices to the skilled labor shortages that have driven wages up. Understanding these elements not only offers a clearer picture of the challenge but also empowers prospective homeowners with knowledge that could potentially save money.
Join us as we explore these critical facets of home building, unraveling the complex tapestry of economics that governs modern construction. Whether you're dreaming of your forever home or simply curious, these insights might just change how you see the bricks and mortar of home building.
- Rising Material Costs
- Labor Shortages Impact
- Regulatory and Compliance Factors
- Technological Advancements
- Cost-Saving Tips for Future Homeowners
Rising Material Costs
The cost of building materials is undoubtedly one of the most significant contributors to the escalating expenses in home construction. Over the past few years, prices for essentials like lumber, steel, and concrete have seen dramatic hikes, attributed to various factors. Global supply chain disruptions, exacerbated by political tensions and natural disasters, have made it harder and more expensive to acquire these necessary resources. For instance, the lumber industry faced a massive price surge post-2020, with costs reaching almost triple their usual rates, driven by both high demand and a marked shortage in supply.
Another pivotal reason behind these rising costs is the fluctuating demand and supply equations energized by economic conditions. With the onset of the COVID-19 pandemic, people started investing more in personal spaces, increasing the need for new homes and renovations, which bred higher demand for materials. At the same time, production and transport logistics had not fully recovered, leading to this supply crunch. Even before the pandemic, construction material prices were on an upward trend due to rising global infrastructure projects.
According to the National Association of Home Builders, "Lumber prices have added about $36,000 to the average cost of a new single-family home, accounting for a sizeable portion of the inflated price tag potential homeowners face today."
Environmental concerns also play a role in the increasing construction budget needed with more expensive eco-friendly materials gaining popularity. Builders often need to choose sustainable options, which sometimes come at a higher price due to the technology and processes involved in creating them. The transition to these alternatives is one supported by modern regulations and an increasing consumer preference for green homes, adding another layer to the cost puzzle.
Lastly, global market trends and geopolitics also have their say in how material costs evolve. Trade tariffs, for instance, can lead to sudden price increases when nations impose restrictions or penalties on the export of steel or aluminum - metals that are integral to the house building process. Such economic policies have a ripple effect across the industry, directly impacting the wallet of the future homeowner. Understanding these factors is essential for anyone looking to build, as it highlights the intricate tapestry of reliance on global systems that most might not initially consider.
Facing these hurdles, it's crucial for prospective builders to be strategic. Some recommend purchasing materials ahead of time when possible or locking in prices through contracts to evade last-minute surges. By grasping the realities behind new home expenses, stakeholders can better prepare financially, leaving room for creativity instead of constraint.
Labor Shortages Impact
One of the most significant pressures on the cost of building a new home today is the severe shortage of skilled labor. This shortage has been growing for years due to multiple contributing factors. A combination of an aging workforce, fewer young entrants into trades, and increased demand from both residential and commercial sectors has created a perfect storm. As experienced workers retire, there aren't enough new tradespeople to fill the gap, causing labor costs to rise dramatically. This increase in wages is passed on to the homebuyer, making the dream of building a new house more expensive.
The impact of the labor shortage extends beyond just higher costs. Projects are frequently delayed, sometimes by months, as contractors struggle to find enough skilled workers to meet their timelines. This not only frustrates homeowners but also disrupts the financial schedules of builders, leading to potential financial losses and increased pressure on those working within the industry. An interesting survey by the Association of General Contractors found that 81% of construction firms reported difficulty in filling hourly craft positions, a stark statistic that illustrates the scope of this issue.
Construction budget management becomes trickier under such constraints, as contractors are forced to offer higher pay to attract the skilled labor they desperately need. This scramble to secure labor has led to some creative hiring practices, with some companies opting to provide additional training to less experienced workers. But this comes with its own set of challenges, primarily the time and financial investment needed to bring these workers up to speed, which ultimately adds to overall project expenses.
In response to labor shortages, some builders are turning to new technologies to bridge the gap. Automation and prefabrication are increasingly seen as viable ways to lessen dependency on human labor. These methods allow for faster and potentially cheaper construction, though they require significant initial investment and a shift in conventional building practices. It's an evolving landscape, with both risks and rewards, as the industry grapples with how best to incorporate these new solutions. A report illustrated that despite short-term hurdles, long-term savings from technology adoption are significant.
"The skilled labor shortage is not just a numbers game; it changes the entire landscape of the construction industry," explains David Cruz, CEO of a prominent construction firm. "We have to rethink how we approach projects, from planning and budgeting to execution and delivery."
Still, for those looking to build their own homes, understanding these dynamics is crucial. Prospective homeowners are advised to plan for longer timelines and to be flexible with scheduling to accommodate potential delays. Another tip is to engage builders known for maintaining good relationships with subcontractors, as they are more likely to secure the needed workforce. Such builders often have a pipeline of reliable tradespeople, which can make all the difference in keeping construction on track and within budget. It's about weighing the costs against the inevitable delays and being prepared to adapt as the situation evolves. Patience and due diligence can go a long way in navigating these labor-related challenges in today's homebuilding landscape.
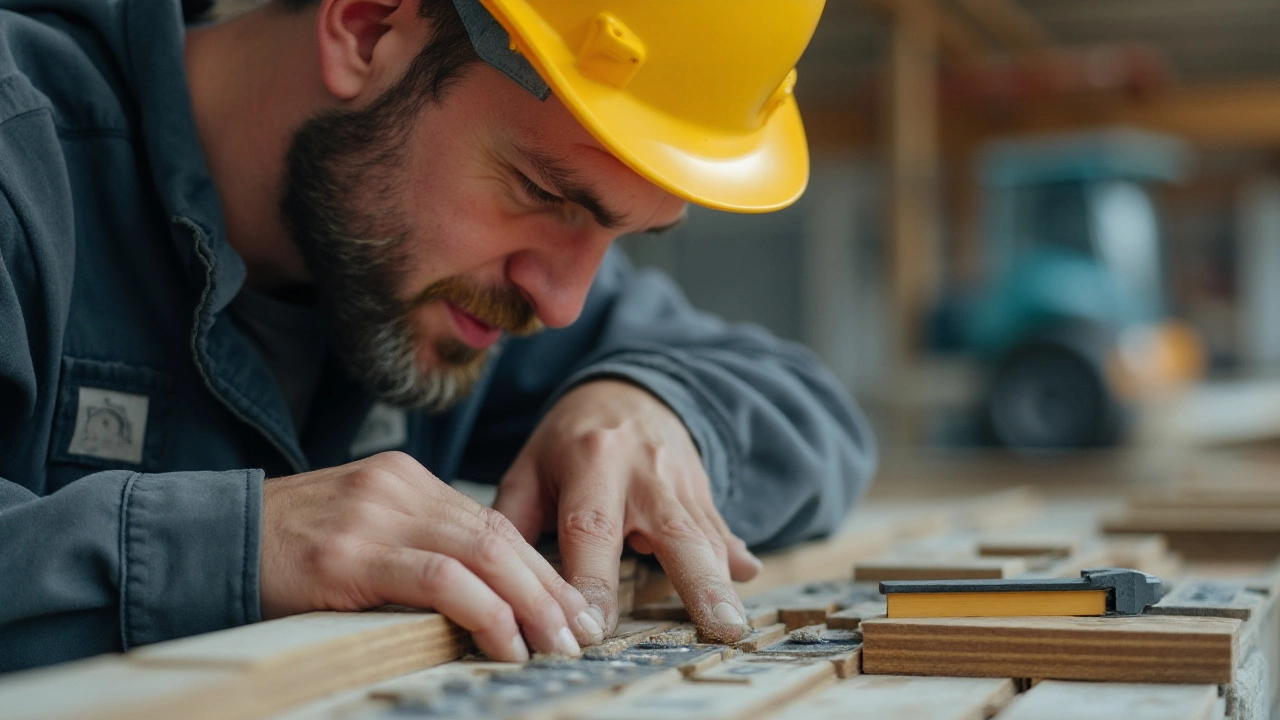
Regulatory and Compliance Factors
When considering why building a new home can be so expensive, it’s essential to recognize the significant impact of regulatory and compliance factors on the overall cost. Building codes, zoning laws, and other regulations play an invaluable role in ensuring safety and environment-friendly construction, but they often contribute to rising costs as well. Each region or locality has its own unique set of building codes that a builder must follow, and navigating this landscape requires time, effort, and money. For instance, acquiring the necessary permits is not just a bureaucratic step but often involves a deep dive into a myriad of technical requirements, sometimes specific to the type of material or structural design being used.
Compliance with these regulations requires meticulous planning and often involves the hiring of specialized consultants or experts who can ensure all requirements are met, adding to the overall house building costs. With increasing attention on sustainable and eco-friendly practices, new builds frequently come under scrutiny to meet energy efficiency standards. Installing efficient insulation, solar systems, and advanced HVAC units can be a hefty financial burden on prospective homeowners, but they are necessary to meet modern standards. This drive towards efficiency is not unwarranted, but its initial costs are significant.
In densely populated urban areas, zoning laws dictate not just the type, size, and location of buildings but also influence the aesthetics and functional aspects of a new build. In some cases, homeowners encounter added costs dealing with these restrictions. Altering any part of the build to comply with a zoning regulation can lead to delays, redesigns, and unexpected financial demands. Dr. Raymond Fletcher, a respected figure in urban planning, succinctly put it,
"The balance between innovation in design and regulatory compliance is often fraught with financial concessions."
Moreover, the ongoing changes in standards necessitate that builders keep up-to-date on regulation shifts, which can vary significantly from year to year. In recent times, there has been a push for inclusive design ensuring accessibility for all individuals - this is a commendable achievement but one that calls for additional structural design considerations and costs. Builders must ensure homes have accessible entries, exits, and facilities which can mean more space, specialized equipment, or innovative architectural solutions. While these requirements enhance the quality of life and accessibility, they also incrementally add to the new home expenses.
Perhaps one of the more challenging aspects of managing construction budget related to regulations is the uncertainty and variability across different regions. No one-size-fits-all solution exists, necessitating tailored approaches that consider the regulatory context of each specific area. The situation is further complicated by potential fines and penalties that can arise from non-compliance. Failing to align with these regulations could not only halt a project but could lead to costly legal battles or requirement to make extensive modifications, further burdening the budget.
Technological Advancements
In recent years, the home building industry has become increasingly intertwined with emerging technologies, and this nexus has been a double-edged sword when it comes to costs. On the one hand, new technologies can significantly boost efficiency and sustainability. On the other, they can inflate the initial costs of construction. Innovations such as smart home devices, energy-efficient systems, and the integration of advanced building materials like self-healing concrete are becoming standard in many new builds. These advancements come with a premium that reflects their cutting-edge nature and the research and development costs that accompany them.
Consider the rise of energy-efficient systems, which are designed to decrease long-term utility bills and carbon footprints. While they promise savings over the lifespan of the home, their installation can involve high upfront expenditure. Technologies like geothermal heating or solar photovoltaic panels require skilled labor and specialized parts, contributing to the escalating initial build cost. Such systems represent a growing segment in new builds, with homeowners increasingly valuing ecological sustainability and governmental incentives aiding adoption rates.
Another key factor is the smart home devices that offer convenience and security. Integrated systems controlling lighting, temperature, and security through a single interface are no longer seen as luxury items but rather necessary amenities for modern living. These systems transform everyday living spaces into connected environments, but they require significant investment from the outset. The complexity of installation and the required support infrastructure for these systems add layers of cost that traditional homes don't demand.
Despite these costs, technological innovations can also drive efficiency during the construction process itself. Tools such as 3D printing and Building Information Modeling (BIM) have revolutionized how buildings are conceptualized and erected. For instance, 3D printing of building components can reduce material waste and labor costs by producing parts on-site. Similarly, BIM allows for detailed visualization and management of construction projects, leading to significant time and cost savings by preemptively resolving design conflicts and streamlining workflows.
Interestingly, the construction industry's shift towards using drones and robotics is also notable. Drones provide an aerial perspective, invaluable for inspection and surveying, while robots handle repetitive or dangerous tasks, reducing risks and potentially cutting costs. These technologies promise increased safety and precision but require significant investment in equipment and training. As these technologies continue to evolve, they will likely play a substantial role in shaping future construction landscapes, potentially leveling out cost burdens as efficiencies grow.
Emphasizing the importance of why technological advancements matter, industry expert Dr. Diana Lin said,
"Technological advancement is the key to unlocking new efficiencies in building, but these advancements do not come cheap initially. The challenge is to balance the cost of innovation with its long-term benefits."Ultimately, while these ongoing developments present an upfront cost hurdle, they also highlight the potential for future savings and enhanced performance, creating a compelling, though financially challenging, narrative for home builders today.
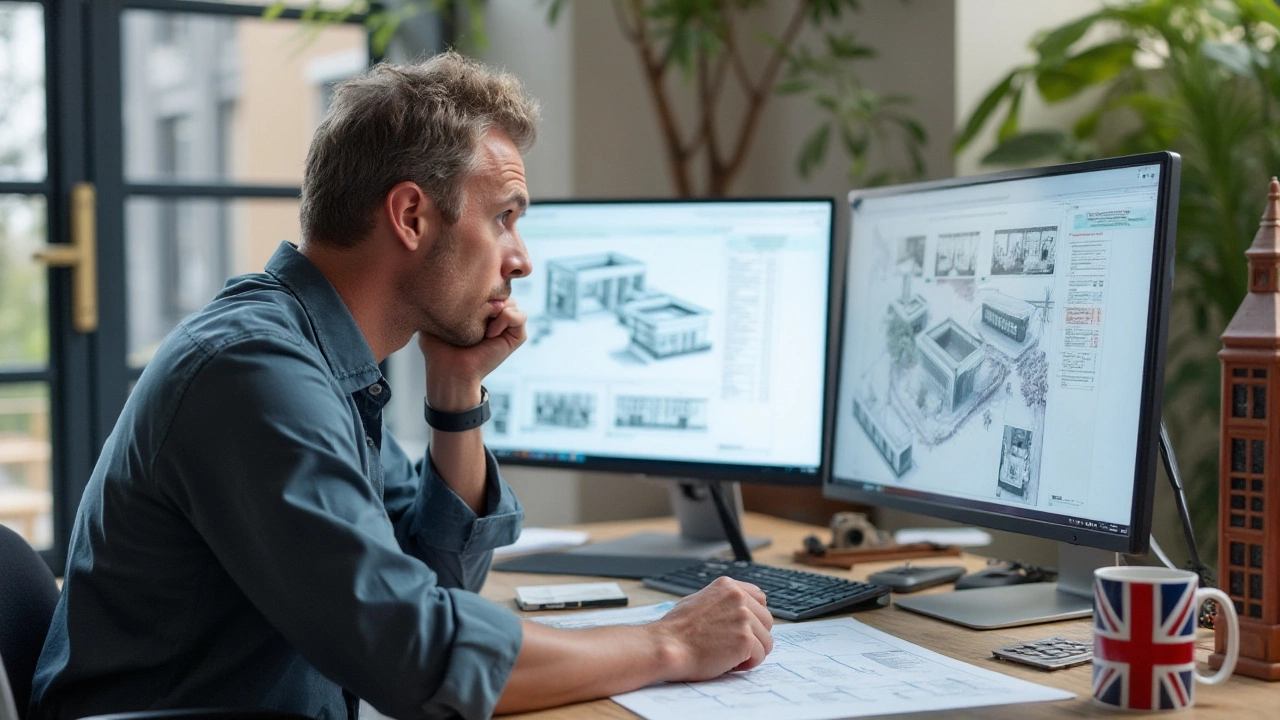
Cost-Saving Tips for Future Homeowners
Building a house doesn't have to be an unattainable dream even with the daunting specter of surging expenses looming large. Future homeowners can take impactful steps to prudently manage their budgets without compromising on their vision or quality. Understanding the dynamics that drive house building costs is essential, but it's equally crucial to identify strategic areas where expenses can be curtailed. One of the primary ways is to carefully consider and plan every aspect of your home design. Open, simpler designs not only use fewer materials but also require less labor to construct. You might be tempted by intricate layouts or extravagant features; however, opting for simplicity can reduce costs significantly.
Moreover, choosing a reliable yet cost-effective location for your build can make a striking difference in your budget. Land prices vary widely based on location, so researching areas where property is more budget-friendly without sacrificing the amenities you desire is a wise move. Another valuable tip is securing fixed-price contracts wherever possible. These contracts can lock in costs, minimizing the risk of exceeding your budget due to fluctuating market prices. Also, consider reaching out to multiple suppliers and contractors. Getting multiple quotes not only helps you secure a competitive price but also ensures that you're fully informed about what's on offer, potentially saving a considerable sum.
An often-overlooked aspect is the use of sustainable and energy-efficient materials. While the initial investment may seem steep, their long-term savings and benefits cannot be underestimated. Homes equipped with solar panels, high-efficiency HVAC systems, or smart home technology systems reap rewards over time through lower utility bills. An investment now can equate to significant savings in the future. Also, think about the timing of your build. Construction costs tend to fluctuate throughout the year, with peaks often occurring in warmer months. Scheduling your build during the off-peak season can help reduce costs, as contractors might offer better rates to maintain steady workflow throughout the year.
Sourcing materials locally is another pragmatic step for trimming expenses. By choosing locally produced materials, transportation costs are reduced, and you might dodge potential delays due to long-distance shipments. Many find that local materials can offer unique, rustic charm, aligning well with both budget and aesthetics. Consider a strategy that many savvy builders employ: doing some of the unskilled labor or finishing work yourself. Tasks such as painting, landscaping, or laying flooring can be immensely rewarding DIY projects. Not only do you save money, but you also add a personal touch to your dwelling. As the legendary architect Frank Lloyd Wright once remarked, "An architect's most useful tools are an eraser at the drafting board and a wrecking bar at the site." Simple, thoughtful changes can often yield profound results.